5 Ways to Prevent Concrete Cracking
When constructing a building, the last thing you want to consider is the potential for cracking and other damage. However, concrete degradation and cracking are common side effects of construction. They’re especially prevalent in outdoor structures exposed to moisture, UV radiation, and freezing temperatures.
Cracking can occur almost any time during a structure’s lifespan—even before it’s built. For example, minute fissures can develop during the concrete mixing process due to different pH levels or calcium chloride contamination. If left unaddressed, these fissures grow wider with time and expose the raw materials inside the concrete frame.
Let’s take a look at five ways that you can prevent cracking:
1. Use quality concrete
Concrete is a mixture of cement, water, and aggregates such as gravel. The cement acts as the binding agent in the concrete, while the water helps combine these materials. Concrete is a durable construction material used to make everything from sidewalks to bridges. However, not all concrete is created equal.
Three basic types of concrete used in modern construction:
- Normal-weight concrete is the standard, with a typical density of around 2,200 lb/ft3. It’s suitable for most applications and has good strength and durability.
- Lightweight concrete has a density of 1,800 lb/ft3.
- Ultra-lightweight concrete has a density of 1,500 lb/ft3. It’s less costly to produce and easier to transport and place.
However, these types of concrete are also less durable than normal-weight concrete. It has a shorter lifespan, is more susceptible to cracking, and can break down faster.
2. Use chemical sealants
A chemical sealant is a type of sealant used for concrete curing. Chemical sealants are water-based, solvent-based, or solventless systems. They’re applied to the surface of the concrete to help it dry more quickly, reduce cracking, and improve its overall strength. You can use chemical sealants to prevent water from getting into small cracks in the concrete.
Once there, the water can freeze and expand, potentially causing more damage to your structure, such as spalling. Chemical sealants are often used in conjunction with curing compounds, which are applied to the surface of the concrete while it’s still wet.
Curing compounds help to prevent moisture trapped in the concrete from expanding, thus reducing the potential for cracking. As curing compounds are water-based, it’s important to dry the concrete thoroughly before applying any sealants.
3. Utilize Epoxy or Urethane Coating
Epoxy or urethane coatings are another great way to prevent concrete from cracking. These coatings are applied to the surface of the concrete to prevent water from getting into the cracks. Once there, it can freeze and expand, causing damage to the surrounding concrete.
Epoxy and urethane coatings are more expensive than chemical sealants but more effective at preventing damage. They also have the added benefit of reducing noise pollution and glare. They’re commonly used to coat the floors of walkways, driveways, and around swimming pools.
4. Install a steel reinforcing mesh
Steel reinforcing mesh is a grid-like structure placed alongside the concrete from the beginning of the mixing process. When mixed with the concrete, the mesh helps to reinforce the structure and prevent cracking. Steel reinforcing mesh can be used in both interior and exterior concrete applications. It’s often installed underneath roadways, sidewalks, and foundations.
The mesh can be placed in the concrete before or after it’s been poured. Before pouring, the most common method is to place the mesh inside a wooden frame, which is later removed. When the mesh is placed amidst the concrete, it’s called “in-situ” mesh. This method is more expensive but also more efficient, as less material is required.
5. Add an extra layer of concrete on top of exposed surfaces
If the concrete frame is already built, you can still prevent cracking by applying an extra layer of concrete on top of the exposed surfaces. This helps prevent water from getting inside the concrete frame, which could freeze and expand. This type of repair is best suited for highly exposed surfaces, such as walkways and driveways.
As the surface will be denser than the surrounding concrete, you’ll need to use a special concrete mixing technique for this repair. Depending on the thickness of the applied layer, you may even have to break the surrounding surface.
Concrete cracking is common, but it doesn’t have to be inevitable. The best way to prevent cracking is to select the right materials and design. You should also take steps to maintain your concrete structures. These include keeping the surrounding area as clean as possible, repairing any damage promptly, and applying protective sealants and coatings where appropriate. By employing these strategies, you can prevent these unwanted concrete defects from occurring and extend the lifespan of your structures or get concrete repair products to fix them.
Call us at 631-298-6300 to learn more.
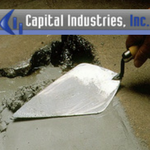
Capital Industries, Inc. is a leading supplier of commercial and industrial concrete repair products. For over 30 years, we have proudly serviced contractors, factories, warehouses and distribution centers for industrial, institutional and commercial customers. We carry a full range of concrete repair materials, including those specifically designed for low temperature areas such as freezers and coolers. Our floor repair products are rapid hardening, allowing you to reopen repaired areas with minimal downtime. All of our products are designed to be used by in-house maintenance personnel and come with an ironclad 100% guarantee of satisfaction.